Behind every sharp-dressed cadet is a hardworking tailor.
Unsung heroes on post, employees in the tailor shop tackle monumental and vital tasks: Tailoring, repairing, and restoring thousands of uniforms for cadets, faculty, and staff. The list of items they tailor is long: Blouses, coatees, overcoats, white ducks, trousers, shirts, skirts, flags, and every variation of them. The shop estimates they alter around 20,000 garments each year, from the small task of adding a button to altering a coatee.
“It’s 12 ladies that take care of all that, and that’s pretty amazing,” said Cindy Dudley, the manager of the tailor shop and a VMI tailor for almost 30 years.
“There’s a lot more to tailoring than meets the eye,” Dudley explained. “Tailoring a garment can range from something that takes two minutes, like putting a button on, to something that honestly takes about eight hours. For example, a tailor could stay on a garment like a coatee all day long to do what she’s supposed to do: Altering it, putting rank on it, the collar, stars, everything.”
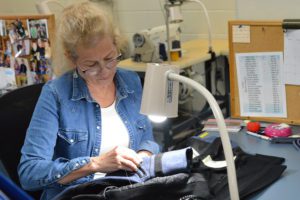
VMI’s Tailor Shop employees work hard to keep cadets, faculty, and staff looking good in their uniforms. Each summer, employees hand-sew new ranks on 500 cadet uniforms.—Photo by Eric Moore, VMI Communications & Marketing.
An example of their efforts is adding rank to uniforms. At the end of the spring semester, cadets turn in their uniforms. The shop reviews and tailors each of the uniforms over the summer. Of those, around 500 cadets receive rank for the following academic year. The tailor shop hand-sews rank on to each of these uniforms.
Working as a tailor requires a lot of training. Donna Runkle has been with the tailor shop for 37 years, and she serves as the trainer for new employees. She explained that garments go through many cycles throughout a cadetship, and it takes roughly three years for a tailor to learn all the aspects of the job thoroughly. In addition, each tailor learns to have a healthy dose of patience in the work.
“I don’t care if you’ve been in here 40 years. You’re gonna have that garment that just will not work,” Dudley joked. “You just have to be patient.”
The tailor shop works hard to ensure that every garment is excellently tailored. This can be quite challenging given the wide range of cadets.
“You have 1,700 cadets, and you’re gonna have all body types,” Dudley explained. “God didn’t make us all alike, so we’re all different. It could be a little bit of everything: Super tall, super short, broad shoulders, tiny waists, sleeves, and legs being different lengths. Some of them have been challenging but interesting. It’s unique and almost fun.”
“We have to figure something out, but then it ends up looking real nice and good on the cadet.” Runkle added.
Over and over, Dudley and Runkle highlighted that the shop does the work they do to serve cadets well. They love the cadets, and they enjoy having them come through the shop.
“You think, ‘That could be my child,’” Runkle said. “I want them to look nice when they go out somewhere.”
“We treat them like we would want to be treated,” Dudley added. Their efforts show and the shop is very proud of their work and the impact they make on post.
“I do feel like I make a difference,” Dudley said. “I like seeing the cadets when the garments fit … It makes you feel good about what you do. That’s what I like about sewing. You can take something that maybe doesn’t fit somebody so well, and when you get done, it’s a near-perfect fitting garment. They look good, and that’s rewarding.”